Learn more about this case study and discover how using our excellent warehouse facilities in the Netherlands improved efficiency in our clients supply chain!
Client: Manufacturer and supplier of power tools with factories in Asia.
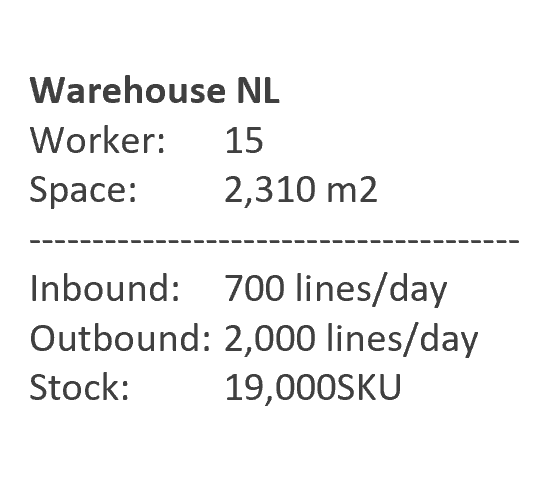
In this case study example, our customer previously used several warehouses in the EU and each of their factories needed to supply parts to each warehouse (RDC: Regional Distribution Center).
Their lead time from warehouse to customers was good, but they had to do stock management at each warehouse location, leading to increased costs.
Firstly, our expert team conducted an investigation into the clients logistics flow. We then made suggestions on how they could optimize their supply chain.
We proposed the customer uses one centralised warehouse (EDC) in the Netherlands. In contrast with the previous scenario, this set up provided many benefits to our customer!
Our customer can ship out their goods to EDC by consolidated unit, allowing them to significantly reduce their transportation costs.
Our solutions makes it easier to control stock compared to the previous scenario of having several regional warehouses.
While EDC leadtime can often be longer than RDC, our EDC is located in the Netherlands where there is easy access to most EU countries. This ensures that there are no major impacts on leadtime.
VAT deferment systems can be applied in the Netherlands.
For more information on our success stories please contact our sales team and discover how LOGISTEED Europe can improve your business.